Making the right Choice for Plating
Pick your plater like a spouse
It’s something you’ll have to live with the rest of your life. So you’d better base the relationship on a strong combination of love, admiration, romance and sex appeal. Your wife? Husband? Sure. But we’re really talking about plating the parts of your beloved machines.
When you’re ready to send some of your valuable castings out for plating, keep in mind that the resulting quality will vary from shop to shop. Electroplating is a complicated process and is plagued with variables. The significant steps, such as the chemical baths, bath temperatures and current voltages must be held to a narrow margin of error. It’s a classic case of “you get what you pay for,” or more emotionally, you’d be smart to pick your plater like you’d pick a spouse.
To take you through the steps, in most cases your castings will need to be cleaned and stripped of the old plating. Good platers will electro-strip your part using a process similar to plating, only in reverse. A cheaper way to do the job (which can be dangerous to your castings) is to grind and sand your parts to quickly remove the old plating. Unfortunately, this time-saving process could sacrifice the detail in your parts by over-grinding, and even make them look like re-casts.
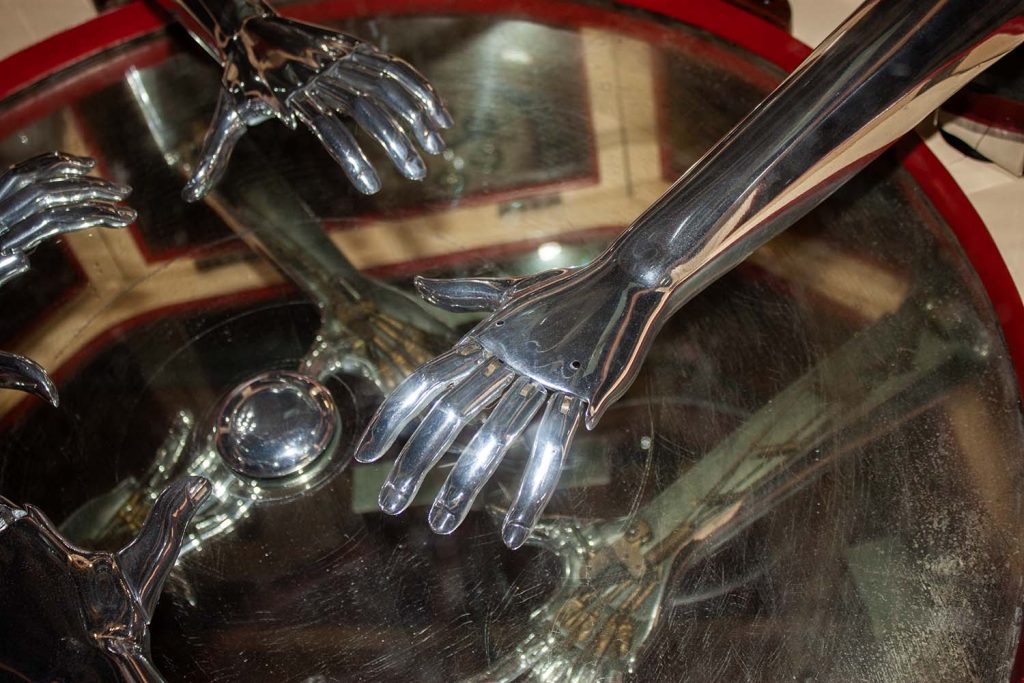
The most important step at this stage is polishing. This is usually what separates a good plater from a not-so-good one. Good platers will take the time and care that is needed to carefully polish the part. By using different polishing wheels and different compounds your parts can be polished to perfection without losing the detail in the castings. Inexpensive shops tend to do a quick once-over job with a large polish wheel, neglecting the tiny areas and difficult corners. When the part is later plated these neglected areas look crusty and dirty, detracting from your overall restoration and repair.
Another problem area to watch out for is the fact that during the polishing process the compound in the wheels flies off in every direction, including the back of the casting and inside any tapped holes. If the plater doesn’t take the time to clean this compound off completely you will have to chase your tapped holes with the proper die and clean the back of the part, all after plating.
Don’t be afraid to ask questions. If the quote seems too low, be careful. Cheap price, cheap job. The difference in cost can usually be justified by the increase in the value of your restored machine.
So much for plating. Now, if you don’t have a spouse, follow the same rules in life and love. Ask questions and do a lot of polishing. And if you do, there are a few tips here that can make life beautiful.
John Papa is both a fixer and a philosopher. He’s great at finding, fixing, restoring, maintaining and selling jukeboxes and other vintage coin machines.